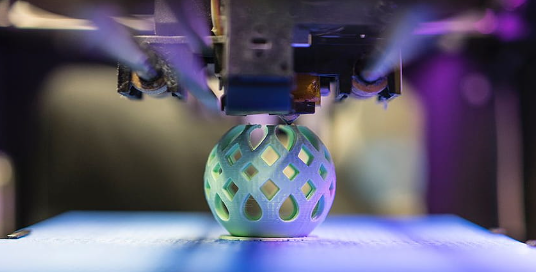
How 3D Printers Work: From Idea to Object
Introduction: How 3D Printers Are Shaping Tomorrow’s World
One ground-breaking creation that has captivated the interest of inventors, engineers, and fans alike in a world where innovation and technology are continuously evolving is the 3D printer. These incredible machines have evolved into more than just tools; they are the first signs of a new age in design and manufacturing. This blog post will take you on a voyage into the world of 3D printing, where we’ll explain the principles, investigate the possibilities, and discover how these technological wonders are changing the way we design, create, and use the things around us.
In a world where technology and creativity are always changing, one ground-breaking creation that has the attention of engineers, enthusiasts, and innovators alike is the 3D printer. These amazing gadgets are ushering in a new era in production and design, transcending beyond simple tools. This blog post is an exploration into the core of 3D printing, where we will unravel the mysteries, discover the opportunities, and comprehend how these technological wonders are revolutionizing the way we design, manufacture, and use the things around us.
We’ll start by going over the fundamentals of 3D printing and looking at the internal mechanisms and essential parts that give these devices their functionality. Next, we’ll look at the complex process of turning a computer model into a physical object and talk about how important slicing software is in the whole process. We will also examine the many 3D printing technologies, each with its own special methods, materials, and uses.
The blog article will also cover the difficulties experienced by experts and enthusiasts with 3D printers and offer advice on upkeep and troubleshooting. We’ll also talk about the fascinating world of do-it-yourself 3D printers and provide advice for anyone who wants to take on the challenge of creating one. You will acquire a thorough grasp of the technology that is revolutionizing the way we develop, create, and manufacture as we delve deeper into the realm of 3D printing. This technology has the potential to completely transform industries and have an impact on our daily lives that we are only now starting to realize.
Section 2: The Printing Process
The 3D Printing Process: Converting Virtual Dreams into Actualities
Layer by layer, a transformative process at the core of 3D printing turns digital designs into tangible objects. Additive manufacturing is a remarkable process that has transformed a wide range of industries, including aerospace and healthcare, and captured the interest of creative thinkers across the globe. We will examine the nuances of the 3D printing process from beginning to end in this section, providing insight into how this technology is influencing society going forward.
Digital Design:
The process starts with a digital design that acts as the object’s blueprint before it is printed. Usually, 3D scanning or computer-aided design (CAD) software are used to create this design. It specifies the final product’s dimensions, form, and details.
Slicing:
The digital model needs to be divided into a large number of horizontal layers before a 3D printer can actually print the design. This important step is handled by specialized software, which creates a set of instructions that direct the printer throughout the manufacturing process.
Material Selection:
Selecting the right material is essential. Many materials, such as plastics, metals, resins, ceramics, and even organic compounds, can be used with 3D printers. The chosen material is determined by the final object’s intended use and desired properties..
4. Printing:
After cutting the design and positioning the material, the 3D printer starts to operate. Depending on the kind of 3D printer, the procedure is different, but the basic idea is always the same: material is deposited layer by layer to build the object. It’s like constructing a structure, where you start at the bottom and work your way up.
Cooling and Solidification:
In order to cure and solidify the material, heat or UV light are frequently used in 3D printing processes. The structure of the object is gradually constructed as each layer is deposited and fuses with the one before it. Accurate solidification is ensured by UV lamps and cooling systems..
Removal and Post-Processing:
The item is carefully taken out of the printer after printing is finished. Sanding, painting, or assembly are examples of post-processing steps that may be required to achieve the desired final product, depending on the complexity and desired finish.
Despite its complexity, 3D printing has unmatched benefits in terms of waste reduction, quick prototyping, and customization. Its uses in everything from fashion and art to aerospace and medical demonstrate the limitless possibilities of turning digital visions into tangible realities. We will examine the uses of this technology as well as the creative ways it is reshaping different industries as we dig deeper into it.
Section 3: Types of 3D Printing Technologies
Types of 3D Printing Technologies: A Diverse Landscape of Innovation
Instead of offering a single, universal solution, 3D printing technology is a broad range of printing methods, each with its own special applications, materials, and guiding principles. We will examine some of the most well-known 3D printing technologies in this section, highlighting the variations that make them appropriate for particular sectors and use cases.
Fused Deposition Modeling (FDM):
One of the most popular 3D printing technologies is FDM. Layer by layer, the object is created by extruding thermoplastic filament through a heated nozzle. FDM is well-liked by hobbyists and in the creation of prototypes and functional parts due to its accessibility, affordability, and versatility.
Stereolithography (SLA):
The basis of SLA is a liquid resin that, when exposed to ultraviolet (UV) light, solidifies. Layer by layer, the resin is precisely cured by the UV laser as a build platform slowly lowers into the resin tank. SLA is well known for its extreme precision and flawless surface finish, which makes it ideal for complex prototypes, jewelry, and dental models..
Selective Laser Sintering (SLS):
SLS uses a powerful laser to carefully fuse powdered materials, frequently plastics or metals, one layer at a time. Robust, functional parts with intricate geometries can be produced with this process. SLS is widely used in the automotive and aerospace industries to create strong, lightweight parts.
Digital Light Processing (DLP):
Similar to SLA, DLP technology employs a digital light projector to simultaneously cure multiple resin layers. Printing speeds increase as a result of this. DLP is frequently used in sectors like dental and jewelry manufacturing where efficiency and speed are vital.
Binder Jetting:
Using a powder-based technique called “binder jetting,” a liquid binding agent is layer-by-layer deposited onto a powdered bed. The object gets solidified and the excess powder is removed. It is utilized in a variety of applications, from custom figurine creation to architecture, and is renowned for its ability to produce large, full-color parts.
Electron Beam Melting (EBM):
EBM is a metal 3D printing technology that melts and fuses metal powders in a vacuum setting using an electron beam. Preferred for producing dense, high-strength metal parts, it is useful in the aerospace and medical industries for the production of orthopedic implants and other components.
These are but a handful of the many kinds of 3D printing technologies that are currently on the market. With a wide range of applications and industries served, each technology has unique benefits and drawbacks. Understanding these technologies is crucial to maximizing the potential of 3D printing in design, manufacturing, and innovation as it continues to progress.
Section 4:Materials in 3D Printing
Substances in 3D Printing: Creating the Future with a Variety of Materials
Beyond its cutting-edge procedures and technologies, 3D printing’s versatility spans a wide range of materials. The final 3D-printed object’s characteristics, uses, and potential are greatly influenced by the material selection. We will examine the various materials used in 3D printing in this section. Each material has a distinct set of properties and uses.
Plastics:
The most popular material for 3D printing is plastic. Materials such as PETG (polyethylene terephthalate glycol), ABS (acrylonitrile butadiene styrene), and PLA (polylactic acid) are among them. For example, PLA is well-known for being simple to use and biodegradable, which makes it perfect for users who are concerned about the environment and for beginners. Conversely, ABS is highly valued for its robustness and longevity, which makes it appropriate for functional components.
Resins:
Photopolymer resins are used in 3D printing processes based on resin, such as Stereolithography (SLA) and Digital Light Processing (DLP). When these materials are exposed to UV light, they solidify. Because of their excellent surface finish and high level of detail, resins are preferred for complex prototypes, jewelry, and dental models.
Metals:
The manufacturing and aerospace industries are undergoing a revolution thanks to metal 3D printing, which is made possible by technologies like Selective Laser Melting (SLM) and Electron Beam Melting (EBM). Stainless steel, titanium, and aluminum are a few of the metals used to create strong, lightweight, and durable parts.
Ceramics:
A growing field, ceramic 3D printing finds use in the creation of finely crafted ceramics, dinnerware, and even biomedical implants. Ceramic materials are valued for their strength and beauty, and they can tolerate high temperatures.
Composites:
Composites are materials that combine polymers and materials like glass or carbon fiber to create lightweight, highly durable objects. Applications for them range from sports equipment to aerospace components.
Biomaterials:
Biomaterials, like medical-grade polymers or bioinks for bioprinting, are crucial to the healthcare industry. Custom implants, prosthetics, and even artificial organs are made with these materials.
Food and Edible Materials:
Food is another area in which 3D printing is being used. To create elaborate confections and culinary treats, edible ingredients such as chocolate, sugar, and pastes are used.
When it comes to 3D printing, material selection is crucial and depends on the intended use, functional needs, and aesthetics. New materials are continuously being developed as 3D printing technology progresses, opening up new avenues for innovation in a variety of industries, including healthcare, art, aerospace, and more. For individuals who want to use 3D printing to the fullest extent possible in their projects and creations, it is essential to comprehend the wide range of materials available.
Section 5: Challenges and Maintenance
Difficulties and Upkeep in 3D Printing: Choosing the Right Path to Success
A new era of manufacturing and design has been brought about by 3D printing, but there are drawbacks and maintenance issues to be aware of. Similar to any other technological device, 3D printers need maintenance in order to function at their best and produce objects of the highest caliber. This section will discuss common problems that hobbyists and experts with 3D printers encounter as well as recommended maintenance procedures.
Print Failures:
Print failures are one of the most irritating issues with 3D printing. These may be caused by problems such as misalignment, clogged nozzles, or improper settings. Regular maintenance and fine-tuning the printer and software settings can help reduce these failures.
Layer Adhesion and Warping:
It can be difficult to ensure good layer adhesion and avoid warping, particularly when working with materials like ABS. These problems can be helped with by enclosure systems, heated beds, and printer bed leveling.
Material Compatibility:
Certain materials are needed for different 3D printing technologies, and not all materials work with every printer. It’s critical to be aware of your printer’s limitations and to use appropriate materials.
Maintenance:
Maintaining your 3D printer regularly is essential to keeping it in good operating order. This entails lubricating moving components, cleaning the print head, and checking that the belts and gears are tensioned correctly.
Nozzle Clogs:
Clogged nozzles can cause printing to stop. Clogs can be avoided by regularly cleaning the nozzle and by using high-quality filaments.
Calibration:
Accurate printing depends on the printer being calibrated properly. For every print job, this involves fine-tuning the settings, leveling the bed, and calibrating the extruder.
Software and Firmware Updates:
It is essential to stay current with firmware and software updates in order to take advantage of new features and enhance print quality.
Support Structures and Overhangs:
Support structures might be needed for 3D prints with intricate details, overhangs, and complex geometries. Although it can be difficult, removing these structures after printing is essential for a smooth finish.
Post-Processing:
Post-processing procedures like sanding, painting, or assembly might be necessary for some applications in order to produce the desired end result. It’s critical to comprehend the post-processing specifications.
By resolving these issues and keeping up with maintenance, you can prolong the life of your 3D printer and guarantee reliable, high-quality output. A thorough understanding of the technology, troubleshooting techniques, and routine maintenance are essential for advancing 3D printing to its pinnacle of excellence. The skills and knowledge needed to excel in the field are always changing along with it.
Section 6: DIY 3D Printers
Building Your Own Creative Powerhouse with DIY 3D Printers
The appeal of 3D printing lies in its ability to enable creation rather than just consumption of printed goods. With DIY (Do-It-Yourself) 3D printers, you have the rare chance to construct a 3D printer from the ground up or assemble one from a kit. This section will delve into the fascinating realm of do-it-yourself 3D printers, explaining what they are and how they enable enthusiasts to express their creativity to the fullest.
Assembling Your Printer:
A variety of kits with prefabricated parts and fully customizable builds are available for DIY 3D printers. Fitting the frame, fastening motors and belts, and wiring the electronics are the steps involved in assembling your printer. This practical experience offers insightful knowledge about how a 3D printer functions.
Customization:
Being able to tailor DIY 3D printers to your own requirements is one of their many notable benefits. You can select the print bed size, the frame material, and even upgrade parts to improve functionality. With this much control, you can customize your printer to fit your artistic goals.
Learning Experience:
Constructing a homemade 3D printer is a learning experience. You acquire a thorough understanding of the electronics and mechanics of 3D printers. It’s a great way to become knowledgeable about firmware, hardware, and 3D printing as a whole.
Cost-Effective:
Do-it-yourself 3D printers can be an affordable option for folks on a tight budget. You can save money by finding the parts on your own and assembling the machine instead of purchasing one that is already built. It’s a desirable choice for makers, hobbyists, and students.
Community and Support:
The community for do-it-yourself 3D printing is active and cooperative. There are communities, tutorials, and forums where enthusiasts offer advice and share their experiences. This sense of camaraderie can be very helpful when looking for guidance or troubleshooting.
Open-Source:
An abundance of open-source firmware and designs for do-it-yourself 3D printers promote creativity and teamwork. This implies that you have access to a multitude of tools, patterns, and applications to improve your 3D printing experience..
Start Small, Dream Big: